STROLLERS & CAR SEATS
DESIGN & ENGINEERING
I am a Sr. Soft Goods Designer at Goodbaby International where I am making life saving products for children and Infants. You can find Evenflo pieces I designed and patterned in all Walmarts and Targets from carseats to strollers to doorway bouncers.
I manage projects at our China, Mexico, and US production facilities specializing in project sustainability and production efficiency on existing platforms.
​
​
here are some TESTIMONIALS FROM FAMILIES WHO HAVE PUT MY PRODUCTS TO THE TEST. I AM HAPPY TO SAY I WAS ABLE TO HELP PROTECT THESE LITTLE ONES AND MANY MORE FROM INJURY!

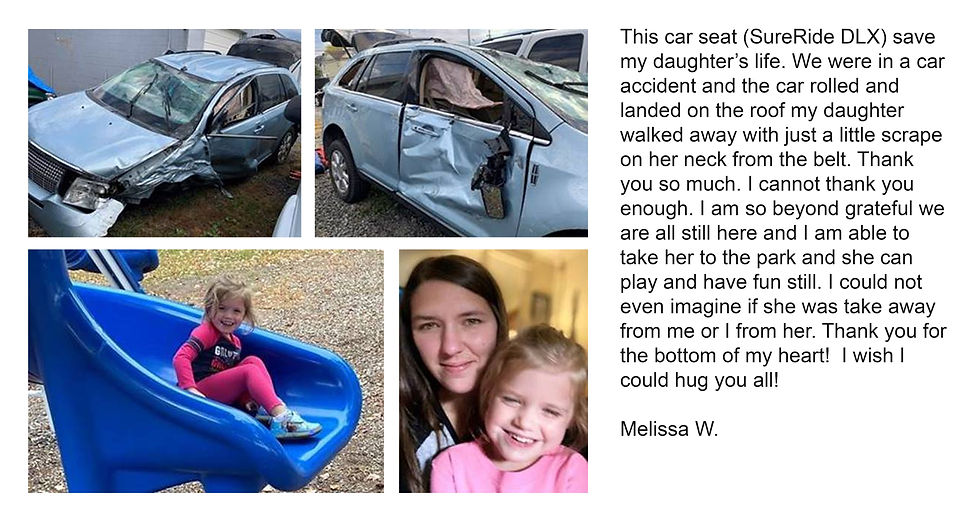


So...

what is a soft goods DEsigner?
Soft Goods Design explores product design that uses materials that are not rigid. Combining the skills of a fashion designer and the design approach of an industrial designer this class creates a unique way to solve a specific set of design criteria.
​
The Soft Goods Engineer will lead design efforts, support the current manufacturing processes, and assist the production manager in maintaining and troubleshooting manufacturing equipment. ... The Soft Goods Engineer must be familiar with soft goods design, manufacturing equipment, processes, tools, and maintenance.
Evenflo Pivot Xplore All-Terrain Double Stroller Wagon. I was the Soft Goods Engineer on this project.
I come into the picture after the initial concept phase is done, when it is time to move from design concept to production-ready.
take the Nurture car seat for example:
I get line drawings with specific color-ways and textile information are provided to me by the Fashion Team.
​
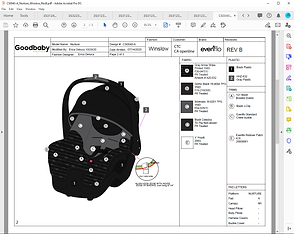.png)
I receive an initial hard goods design concept with a 3D printed seat shell or stroller frame from the Hardgoods Design team.
.png)
The Product and Marketing team provides forecasting to determine order quantities quantity and price requirements.

-Next, I begin to create patterns based off of that shell and the initial design sketches. To make the patterns I use Gerber Patterning Software and AutoCAD, and along with the help of my associate designer we begin to make sewn prototypes. We will make a number of sewn drafts until we have sample with a good fit to the shell.
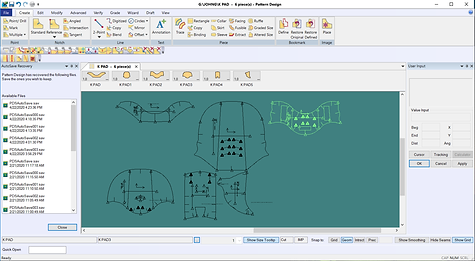.png)
.png)

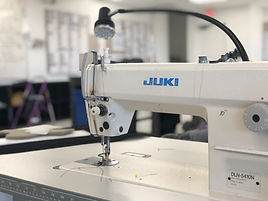
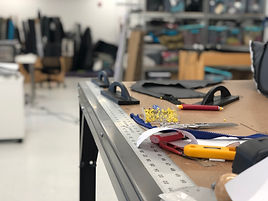
-We review a number of iterations between myself and hard goods designers, safety specialists and quality control to make sure we have a cohesive finished piece. We have to make sure that there is no strangulation or entanglement hazards here. Also making sure that we are aligned on soft goods attachment points that don't interrupt the product's function.
​
_edited.jpg)

-Once we have a somewhat ready design in hand I create a soft goods Bill Of Materials which lists every part inside of the piece and details about them. This document ties into the larger product BOM and is important for procurement and production.
​

woven branding patch


warning label
law tag & care tag
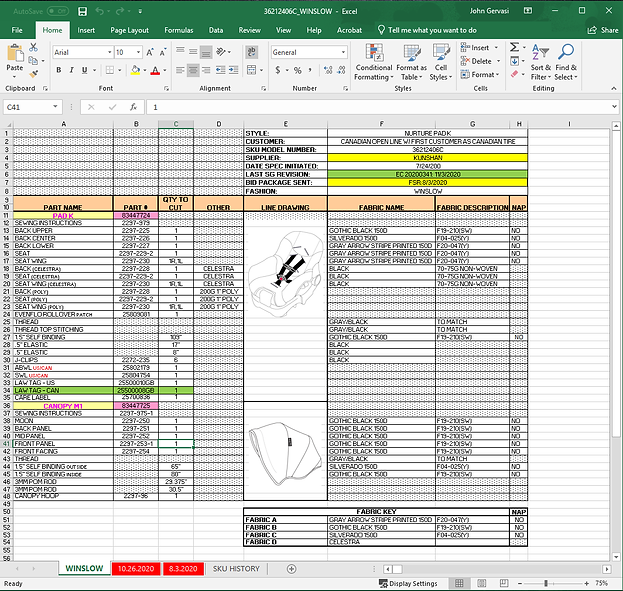.png)
-I create sewing instructions that align with the pattern pieces and the soft goods BOMs. Between those three documents any individual sample maker or production facility would be able to create pieces to completion.
​
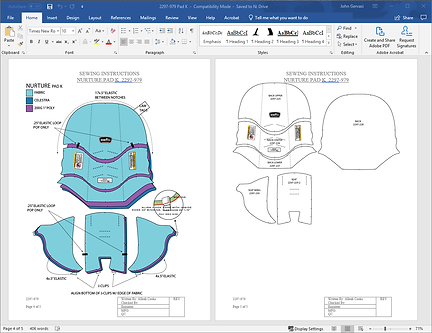.png)
.png)
-These final samples are tested against safety standards and quality regulations based on the regions we sell in. These standards vary between the US, Canada, Europe, and Asia. We make products for babies that are a few weeks old all the way up to booster seats children up to 100lbs. The crash sled is actually a lot like what you've seen on car commercials or myth busters.
.jpeg)
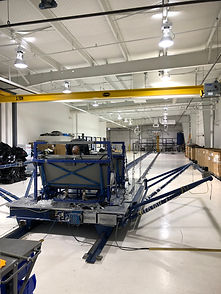

-When we have a final design finished, test-rated and cost approved for production we make something called a Master Aesthetic Sample, or MAS. These MAS's are sent to all the teams that need to sign the Approval Certificate. This confirms that everything checks out and is ready to hit the shelves in stores around the world.
​


